Toyota Production System
Implementing the TPS: Part Two
Relation between 5S and Kanban card system:
Q. Is the location of inventory also important?
A. Each process should have its own inventory. Whenever we have a small lot production, which is conducted if we can't make one piece production, the lot size is small but usually there is a storage location. The workers bring the Kanban card to this storage and they pick up the completed part with their Kanban card installed to each parts box. The kanban card and the indicator plate are different.
Q. Does the Kanban system require the 5S system to be in place?
A. The 5S movement is certainly a prerequisite for the implementation of the Kanban card system. We can not implement a Kanban card system without carrying out 5S. If the inventory is reduced by 5S then it doesn't just mean the reduction of capital cost (interest), but also the inventory itself is holding some amount of fund then if that inventory is reduced then that fund can be pooled, and the cash outlay put into that inventory can be reduced. Furthermore, the production lead-time will be reduced, the lead-time consists of inventory carrying time + processing time and conveyance time.
Q. Once they have finished the Seiri and Seiton they have the 3 other Ss. What about Seiso? Are there any special methods they should adopt for good ways of cleaning?
A. There are many examples of good Seiso. You must devise something to handle the metallic powder created from the machines in order to ensure that this powder does not spread. Seiso involves not just cleaning but also reducing the time spent for cleaning. This is a kind of kaizen. It's the responsibility of the person using the machine to try and reduce the spread of this powder. Furthermore, some machines may also leak oil and some machines are always dirty with metallic powder. In these cases the machine may stop working, break or produce faulty parts. So, Seiso can lead not only to the overall improvement of efficiency but also improve safety as well. If the oil is always leaking then the floor is very slippery and could cause an accident. 5S is not just about reducing costs but also about improving worker safety as well. But from the viewpoint of JIT, I want to emphasize that although there are many good things to come from 5S the most important points are the production lead-time reduction.
Q. What abut Seiketsu and Shitsuke?
A. Seiso, Seiketsu and Shitsuke are all closely related. Seiso, to continually maintain tidiness, depends on Seiketsu which is to standardize cleanup activities so that these actions are specific and easy to perform. Shitsuke is a kind of habit of doing the 5S movement. When we start the 5S movement we should go through the steps one by one, Seiri, Seiton etc., but there must be a kind of cycle. A big Seiri and Seiton project could be done probably twice a year. It is very laborious so people don't like to do Seiri and Seiton but cleaning up is very healthy and good for everybody. However, although people say that the appearance is good it has nothing to do with cost reduction. That is a misunderstanding.
Q. What kind of schedule should the project team set for the 5S milestones?
A. It's not necessary to completely do the 5S in one go. Step by step unnecessary things could be abolished. For instance, in the beginning just 50% accomplishment is OK and then they could gradually continue to complete the rest. There are many things comprising of unnecessary things such as inventory, materials, WIP, jigs, tools, machines etc. We are not required to apply 5S to all of these things at the same time. In addition, we don't have to undertake 5S at all the plants at the same time. First of all, do only one plant, and then next time do another plant.
Motivation:
Q. How often should 5S be performed?
A. We should continuously conduct 5S even if it is not the initial project, otherwise gradually things will return back to how they were before. Rather than trying to do it all in the beginning and then stopping it would be better to start with one part and then continue to keep improving. However, at first we should implement a big 5S movement.
Q. In the beginning it may be easy to improve the shop floor with 5S but as time goes on it will become more difficult to keep improving? What things can they do to keep the 5S going?
A. This is a part of Shitsuke, motivating workers to perform maintenance and continuous improvement activities. Encouragement of the workers is very important but Shitsuke is considered the most difficult part of 5S. One way we could do this is by comparing the past with the present by using point photography (see figure below), a method of taking photographs of the same position from the same direction. These photographs are then continuously pasted on the company notice board for all the workers to see. This motivates the workers to continue improving by evoking feelings of pride or shame in them. However, as things progress it will be harder to make improvements so in each process the supervisor will add comments to show where things can be improved. It is the job of the project team to take these photographs.
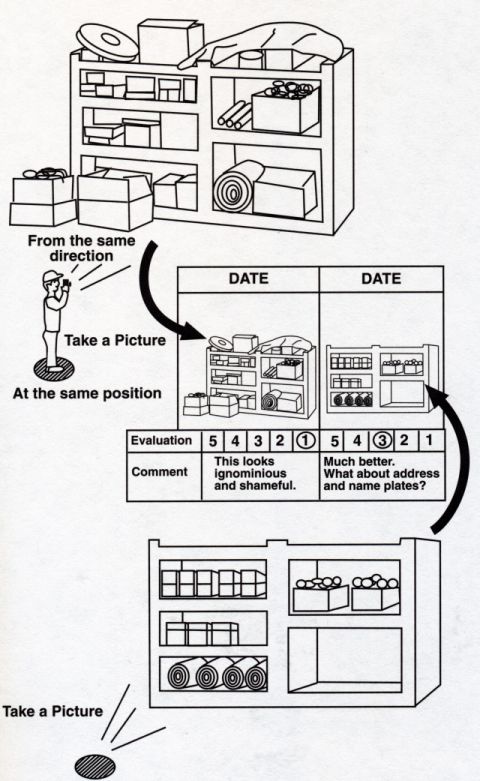
Figure: Point Photography method.
Q. What opportunity do the workers themselves have to contribute to the process?
A. In the beginning the workers must participate in an in-house seminar for TPS itself and 5S as well. Theoretically, their personal goal must be congruent to the company goal. We call this GOALS CONGRUENCE. That is very difficult but important.
Q. What goals should the company establish for their 5S to achieve?
A. One company I know established a space goal. If we remove the unnecessary shelves, machines and inventory etc then we can have more space from where the unnecessary things are removed and free up space. Thus, we can have a space goal (in square meters). Normally, space itself has nothing to do itself with cost reduction, although lighting (energy) may be reduced.
Q. How should the company organize the QC Circle?
A. A Japanese QC (Quality Control) circle is equivalent to a team in the formal routine line. The foreman supervises 3 or 4 teams and each team will have its own team leader. The team leader is not a formal supervisor. The 5S and Kaizen movement is conducted after the regular labor hours, usually 3 times a week after work. It's very laborious, but it takes place for only about a month whilst the 5S is being undertaken.
Part Three of the Implementing the TPS interview coming soon.